The discussion basically originated in the marketplace section where I mentioned that the reason to sell my lathe was a 4 axis CNC router.
CNC with rotational axis and a lathe have different advantages and disadvantages for various tasks.
Machining irregular shape or machining texture on this shape (like snake skin or a bunch of random size half spheres) on the CNC is very doable. If you can draw it, it can cut. (within mechanical limitations of the router) Physical machining is done by the router or a spindle, using various mill (ball mill, tapered mill and so on). Router moves in XYZ axis as well as the stock, slowly rotating in A axis (usual designation for rotational.) So, it is not limited to rotational axial motion of the stock like lathe and there's no need for additional jigs. You can also drill dowel holes. Basically it is very precise carving with the router.
However, it is a fairly slow process. It requires knowledge in 3d modeling
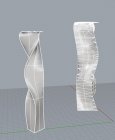
as well as operating CNC router. It's a very high initial investment. The finished surface is achieved by setting small stopover on the final tool.
A lathe can output round parts significantly quicker. If you need to turn a round chair leg or anything of the sort and sand it smooth, lathe will outproduce A axis CNC by a high margin.
There are also CNC lathes. These operate like regular lathe with the exception of the numerically controlled tool feed and automatic tool changers.
CNC with rotational axis and a lathe have different advantages and disadvantages for various tasks.
Machining irregular shape or machining texture on this shape (like snake skin or a bunch of random size half spheres) on the CNC is very doable. If you can draw it, it can cut. (within mechanical limitations of the router) Physical machining is done by the router or a spindle, using various mill (ball mill, tapered mill and so on). Router moves in XYZ axis as well as the stock, slowly rotating in A axis (usual designation for rotational.) So, it is not limited to rotational axial motion of the stock like lathe and there's no need for additional jigs. You can also drill dowel holes. Basically it is very precise carving with the router.
However, it is a fairly slow process. It requires knowledge in 3d modeling
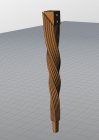
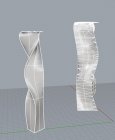
as well as operating CNC router. It's a very high initial investment. The finished surface is achieved by setting small stopover on the final tool.
A lathe can output round parts significantly quicker. If you need to turn a round chair leg or anything of the sort and sand it smooth, lathe will outproduce A axis CNC by a high margin.
There are also CNC lathes. These operate like regular lathe with the exception of the numerically controlled tool feed and automatic tool changers.
Last edited: