I am making a "tripot", three conjoined hollow forms symmetrically arranged around a center. I hadn't worked out how to make the three vessels equal in size and shape beyond making a template, but after shaping the first and considering the problem I remembered that Lyle Jamieson mentioned devising a laser template method. This is what I came up with.
I cobbed together a template support bar from a 3/4" x 4" plywood drop screwed to a short mast held in my outboard tool rest, just above the swing of the eccentric workpiece. I screwed a 1/4" 4" x 12"plywood template blank to the top edge of the horizontal bar and used a construction laser on the lathe ways to shoot vertical lines tangent to the first pot's profile and plot a set of points on the template's underside. I bandsawed out the template curve, remounted it and used the laser on my Bosch hollowing rig to shine points down on the next blank for milling to shape with toolpost mounted grinders. Trent's fine adjuster on the laser housing is very useful for getting a vertical beam of light.
After making this I thought of the hinged finger jigs I have seen in magazines for sizing spindle cuts. I don't think that would work here as the fingers would hang up on the eccentric lobes, but maybe someone else has figured out how to make it work. The laser is not super precise but it gets me pretty close. One could use offsets and outside calipers on some pieces but these lobes are close enough together that I can't mill a full semi-circle, making caliper measurement a bust.
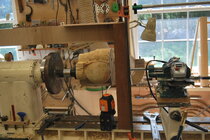
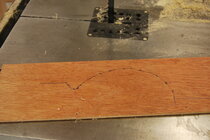
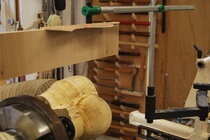
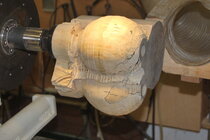
I cobbed together a template support bar from a 3/4" x 4" plywood drop screwed to a short mast held in my outboard tool rest, just above the swing of the eccentric workpiece. I screwed a 1/4" 4" x 12"plywood template blank to the top edge of the horizontal bar and used a construction laser on the lathe ways to shoot vertical lines tangent to the first pot's profile and plot a set of points on the template's underside. I bandsawed out the template curve, remounted it and used the laser on my Bosch hollowing rig to shine points down on the next blank for milling to shape with toolpost mounted grinders. Trent's fine adjuster on the laser housing is very useful for getting a vertical beam of light.
After making this I thought of the hinged finger jigs I have seen in magazines for sizing spindle cuts. I don't think that would work here as the fingers would hang up on the eccentric lobes, but maybe someone else has figured out how to make it work. The laser is not super precise but it gets me pretty close. One could use offsets and outside calipers on some pieces but these lobes are close enough together that I can't mill a full semi-circle, making caliper measurement a bust.
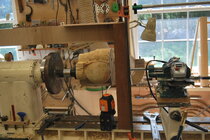
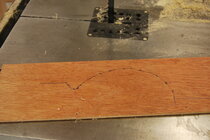
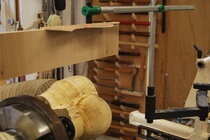
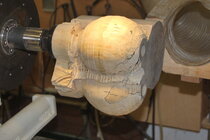
Last edited: