Here are a couple of pics on one approach to large hollowforms some may find of interest:
1) The rigors of hollowing require a faceplate - on a "large hollowform", a 6"
2) Holes should be predrilled to a tightly controlled depth - the outer screws should allow for the curve of the piece - I grind the tips off of 1" screws as the tips add nothing to the holding power.
3) Last step after final hollowing and final shaping is to remove the outer screws - no problem since you're back on the live center
4) Then "dive under" with small gouge, parting tool, and detail gouge to complete the profile
5) Cut the annular ring that will be the base which leaves about a 3" to 3.5" tenon.
6) I then remove the faceplate and mount a floor flange for 1/2" pipe - provides a convenient way to handle for subsequent sanding and finishing operations
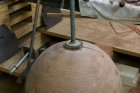
1) The rigors of hollowing require a faceplate - on a "large hollowform", a 6"
2) Holes should be predrilled to a tightly controlled depth - the outer screws should allow for the curve of the piece - I grind the tips off of 1" screws as the tips add nothing to the holding power.
3) Last step after final hollowing and final shaping is to remove the outer screws - no problem since you're back on the live center
4) Then "dive under" with small gouge, parting tool, and detail gouge to complete the profile
5) Cut the annular ring that will be the base which leaves about a 3" to 3.5" tenon.
6) I then remove the faceplate and mount a floor flange for 1/2" pipe - provides a convenient way to handle for subsequent sanding and finishing operations
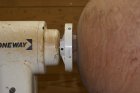
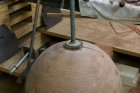