I don't mean to start a post with such a hyperbolic subject line but in this case. I feel it is well deserved. (See bottom for how you can benefit!) 
I've just returned from a 3 day "hat making' session with JoHannes and thought I'd make some comments on it.
I've been turning for about 20 years, making hollow forms, bowls, spindle work and aiming to get....thin.
Given that end goal, I thought the session with JoHannes might teach me some new approaches and give me something to cover my balding head as a result.
I will include a couple of photos of my work only to show that I'm not an utter novice BUT I will say, I felt like an utter beginner in comparison with JoHannes.
I attended the session with another turner (JoHannes likes to have 2 people as a minimum to make the cost more reasonable). The other turner had only recently started turning and so needed to learn about sharpening techniques, tool presentation/body position etc....an eager to learn beginner.
JoHannes was excellent, truly and excellent teacher. He rotated between us and was able to quickly adapt to whatever challenges in approaches we were facing. We BOTH ended up with hats at the end of the process. The days were LONG and JoHannes ended the days when we were all beat (so about a 7.30am start, brief stop for a 30 minute lunch and then work continued until between 6.30 and 7.30 on all 3 days (you get your moneys worth of his time!)
We watched him make a hat on the first day, taking us from log through to completed hat in slow, steps, stopping to show each stage and the choices he was making about tool presentation, tool selection and how to use his innovative light source to gauge material thickness (google that to find it).
We then prepped our own blanks, in readiness for the next day.
I was about 2/3rds of the way into making my hat at the end of the second day, when I made a rookie mistake, picked up the wrong one of the two calipers I was using (tired!) and turned to the wrong dimension. I could have just continued and made a smaller hat but JoHannes would have none of it. He offered to grab a log and "get you to where you are now" before handing over.
This was another WOW! No talking, just him working at his usual production speed. What took me most of a day to do, he did in just over 40 minutes.
MICHELSEN GRIND/VECTOR Fixture
I have my own grind that I've been using. A modification of an Ellsworth/Irish grind with a steep nose and swept wings. I turned up for the class with my own Varigrind setup, ready to reproduce it. JoHannes was fine with that but suggested I try using his tool and grind (I was an early-adopter of Doug Thompson's tools, when Doug first started selling so I knew the steel). I was open to using his grind but not absolutely convinced it would improve over what I was using, with my hand produced relief grinds. Having had an opportunity to use Johannes' grind and the repeatability of his fixture, I ended up switchig, reground my gouges and bought his vector fixture (anyone want to buy a bunch of Varigrinds? ;-*)
One thing I would say about the fixture is that it still needs you to make the grind (just like the Oneway) and so having a reference image was helpful (as was having one of his tools to look at). Once again he was super patient and helpful.
The other purchase I made was his super floppy sanding disks and extensions. I've used long shafts typically used in vehicle polishing to work inside my bowls OR used a Don Pencil (out of business now) version on the lathe with some Beall buffs. I really like what Hannes is having made up in VT. They are inexpensive shafts that match with readily available sanding backing pads. He also takes some of those commercially available pads and machines the back to relieve most of the foam to make a super-flexible backer that works well to sand the various contours of the hat (and will work well with bowls). He charges an extra couple of bucks over the cost of buying the backers for his time in doing the machining....try them.
So, in summary, I am usually reluctant to spend 3 days with anyone; you never know how personalities will mesh, especially when working together. JoHannes was a hoot! He's the life and soul of the party and great fun to be with and genuinely wants to TEACH. You can see from the many hat turners that now sell their products (who learned from JoHannes) that he takes pride in being the innovator in this movement and is happy to see the interest in turning as a result.
If this sounds like an advert, IT IS! I've come to this forum for decades for advice and suggestions and so I feel compelled to make this one. Go for it!
NOTE
While I was there, JoHannes had a student have to cancel his upcoming class, so there is a slot available for Nov/Dec (he's working with the remaining student on dates)
Here's some pictures of my work and the hat I/we made in its bending frame.
I have some remarkable video (slow motion) of JoHannes cutting with the flute of his gouge fully vertical in order to take off those final 64ths. Scared the pants off me when I saw it, but he showed me how to do it with his grind. I will try and find a way to post those large video files and will add it to this post if I succeed.
WWW
WWW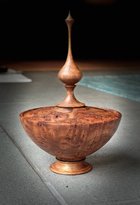
Hats off to you all
Ed
I've just returned from a 3 day "hat making' session with JoHannes and thought I'd make some comments on it.
I've been turning for about 20 years, making hollow forms, bowls, spindle work and aiming to get....thin.
Given that end goal, I thought the session with JoHannes might teach me some new approaches and give me something to cover my balding head as a result.
I will include a couple of photos of my work only to show that I'm not an utter novice BUT I will say, I felt like an utter beginner in comparison with JoHannes.
I attended the session with another turner (JoHannes likes to have 2 people as a minimum to make the cost more reasonable). The other turner had only recently started turning and so needed to learn about sharpening techniques, tool presentation/body position etc....an eager to learn beginner.
JoHannes was excellent, truly and excellent teacher. He rotated between us and was able to quickly adapt to whatever challenges in approaches we were facing. We BOTH ended up with hats at the end of the process. The days were LONG and JoHannes ended the days when we were all beat (so about a 7.30am start, brief stop for a 30 minute lunch and then work continued until between 6.30 and 7.30 on all 3 days (you get your moneys worth of his time!)
We watched him make a hat on the first day, taking us from log through to completed hat in slow, steps, stopping to show each stage and the choices he was making about tool presentation, tool selection and how to use his innovative light source to gauge material thickness (google that to find it).
We then prepped our own blanks, in readiness for the next day.
I was about 2/3rds of the way into making my hat at the end of the second day, when I made a rookie mistake, picked up the wrong one of the two calipers I was using (tired!) and turned to the wrong dimension. I could have just continued and made a smaller hat but JoHannes would have none of it. He offered to grab a log and "get you to where you are now" before handing over.
This was another WOW! No talking, just him working at his usual production speed. What took me most of a day to do, he did in just over 40 minutes.
MICHELSEN GRIND/VECTOR Fixture
I have my own grind that I've been using. A modification of an Ellsworth/Irish grind with a steep nose and swept wings. I turned up for the class with my own Varigrind setup, ready to reproduce it. JoHannes was fine with that but suggested I try using his tool and grind (I was an early-adopter of Doug Thompson's tools, when Doug first started selling so I knew the steel). I was open to using his grind but not absolutely convinced it would improve over what I was using, with my hand produced relief grinds. Having had an opportunity to use Johannes' grind and the repeatability of his fixture, I ended up switchig, reground my gouges and bought his vector fixture (anyone want to buy a bunch of Varigrinds? ;-*)
One thing I would say about the fixture is that it still needs you to make the grind (just like the Oneway) and so having a reference image was helpful (as was having one of his tools to look at). Once again he was super patient and helpful.
The other purchase I made was his super floppy sanding disks and extensions. I've used long shafts typically used in vehicle polishing to work inside my bowls OR used a Don Pencil (out of business now) version on the lathe with some Beall buffs. I really like what Hannes is having made up in VT. They are inexpensive shafts that match with readily available sanding backing pads. He also takes some of those commercially available pads and machines the back to relieve most of the foam to make a super-flexible backer that works well to sand the various contours of the hat (and will work well with bowls). He charges an extra couple of bucks over the cost of buying the backers for his time in doing the machining....try them.
So, in summary, I am usually reluctant to spend 3 days with anyone; you never know how personalities will mesh, especially when working together. JoHannes was a hoot! He's the life and soul of the party and great fun to be with and genuinely wants to TEACH. You can see from the many hat turners that now sell their products (who learned from JoHannes) that he takes pride in being the innovator in this movement and is happy to see the interest in turning as a result.
If this sounds like an advert, IT IS! I've come to this forum for decades for advice and suggestions and so I feel compelled to make this one. Go for it!
NOTE
While I was there, JoHannes had a student have to cancel his upcoming class, so there is a slot available for Nov/Dec (he's working with the remaining student on dates)
Here's some pictures of my work and the hat I/we made in its bending frame.
I have some remarkable video (slow motion) of JoHannes cutting with the flute of his gouge fully vertical in order to take off those final 64ths. Scared the pants off me when I saw it, but he showed me how to do it with his grind. I will try and find a way to post those large video files and will add it to this post if I succeed.
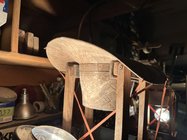
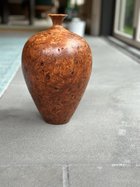
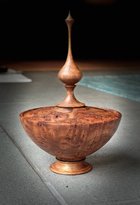
Hats off to you all
Ed