I dove into the vortex when my family gave me a Jet mini lathe about 15 years ago. In a couple years, I adopted a used Powermatic, but I still have the mini lathe and enjoy using it. It's just approachable and calm. Also in a heated space.
Over 4-5 years of occasional use, I've noticed the tail stock lock needing to be swung farther and farther over to secure it. It's at the point where it's in the way of the banjo and something has to be done.
Yesterday, I pulled, and broke, the c-clip holding the locking rod in place and was a little surprised at what I found. The locking rod has an asymmetrically shaped section where the clamping mechanism fits. As I hope can be seen in the photos, this section has been ground and rounded by the hole in the bolt of the clamp. You probably can't see, but the edges of this hole are 'sharpened' and have slightly protruding edges, presumably made during use rather than at the factory. It seems like the locking rod is soft steel and the bolt is harder, hence the bolt has ground down the rod.
In any case, I assume I'll need to buy a new locking rod, which is available from Jet for a tolerable price. Just in case, I'm asking all you experienced folks, is there an alternative to replacing it? Should I replace the bolt as well? (remarkably pricey from Jet) Also, how do I prevent this from happening in the future? Thanks for your help.
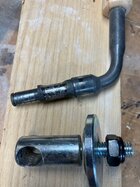

Over 4-5 years of occasional use, I've noticed the tail stock lock needing to be swung farther and farther over to secure it. It's at the point where it's in the way of the banjo and something has to be done.
Yesterday, I pulled, and broke, the c-clip holding the locking rod in place and was a little surprised at what I found. The locking rod has an asymmetrically shaped section where the clamping mechanism fits. As I hope can be seen in the photos, this section has been ground and rounded by the hole in the bolt of the clamp. You probably can't see, but the edges of this hole are 'sharpened' and have slightly protruding edges, presumably made during use rather than at the factory. It seems like the locking rod is soft steel and the bolt is harder, hence the bolt has ground down the rod.
In any case, I assume I'll need to buy a new locking rod, which is available from Jet for a tolerable price. Just in case, I'm asking all you experienced folks, is there an alternative to replacing it? Should I replace the bolt as well? (remarkably pricey from Jet) Also, how do I prevent this from happening in the future? Thanks for your help.
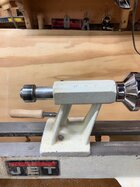
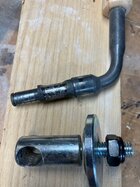