Received the system Saturday, assembled, and watched videos all Saturday night. I should have practiced first but I jumped right into it
.
This one measures 9-1/2” x 5” when I reduce the foot, and the entrance hole is 1-5/8”.
Did a few things right but had a hard time reaching the widest point of the form and I adjusted everything I could think of, the bar would hit the entrance hole and prevent the reach I needed. Not the tools fault but the operator. Top is around 1/8” thick and probably 1/4” at the widest part, bottom is good.
I should have started with a larger entrance hole and maybe not as wide. The important thing is I learned a lot and didn’t do too bad for my first piece. However no one with long fingers will hold the form
. I’ll try the carbide on the next one and try it on a piece of cherry.
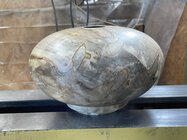
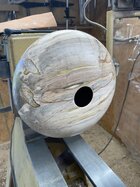
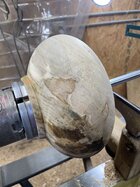
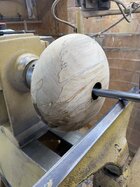

This one measures 9-1/2” x 5” when I reduce the foot, and the entrance hole is 1-5/8”.
Did a few things right but had a hard time reaching the widest point of the form and I adjusted everything I could think of, the bar would hit the entrance hole and prevent the reach I needed. Not the tools fault but the operator. Top is around 1/8” thick and probably 1/4” at the widest part, bottom is good.
I should have started with a larger entrance hole and maybe not as wide. The important thing is I learned a lot and didn’t do too bad for my first piece. However no one with long fingers will hold the form

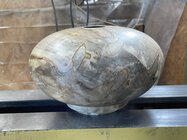
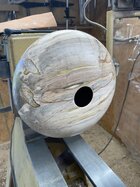
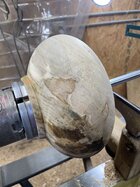
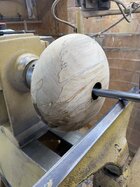