Hello all wise woodturners.
I'm turning some drop spindles. I like them to be edge weighted so that they are lighter and spin well. That means that I hollow out the middle except for a center post that the dowel goes through and the edge. These are 2 1/2" - 3" in width and 3/4" to 1 1/4" in thickness usually. I drill the 3/8" through hole first and then turn them. The problem I'm having is with the thicker ones.
I've tried any number of ways to hold these. I've tried glueing them to the dowel first and clamping that in a chuck. I've tried turning a wooden faceplate with a dowel epoxied into it to register the dowel hole on the piece I'm turning and using double sided tape to hold it to the faceplate.
But these are small, and I'm hollowing pretty deeply without a lot of room and catches happen. When they do, the piece usually is knocked off-center and I have to sort of start over with it. Not to mention the damage done to the dowel if I've glued the whorl on already and am holding that dowel to turn.
I've thought about this a lot, and I don't recall seeing any other way to turn these whorls except for making a little tapered wood button pin and hammering that into the dowel hole and clamping the other side in a chuck. My worry is that doing so will wallow out the dowel hole a bit, and I'd rather use 3/8" birch dowels that I taper for these rather than turning a shaft from scratch. So, the dowels are just under 3/8" already. I don't have any more room for slop. And the button would get in the way of hollowing, making it hard to turn the center post cleanly.
I don't know if a 3/8" collet chuck might do a better job of holding it securely while I turn if I glue the whorl on the dowel first. But I don't have a collet chuck anyway!
Here's my current idea, and I thought I'd run it by y'all and see if you have any critiques or other suggestions. I suspect y'all will know of ways I just haven't come across yet.
I'm thinking of expoxying a length of 3/8" threaded rod into a 1" dowel I turn so that I can clamp it in a chuck, say one with 70mm jaws so there's a nice register for the face of the piece I'm turning. Then, I could drill a hole through a short length of 1/2" or 3/4" dowel as a bushing and put a washer and nut on the other side, so that when I tighten the nut, I clamp the piece I'm turning between the jaws of the chuck and the wood bushing in the center in front. Would this work?
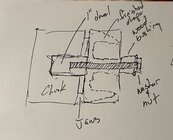
Is there a better way to do this, short of learning how to use my bowl gouge better so I don't have catches?
I'm turning some drop spindles. I like them to be edge weighted so that they are lighter and spin well. That means that I hollow out the middle except for a center post that the dowel goes through and the edge. These are 2 1/2" - 3" in width and 3/4" to 1 1/4" in thickness usually. I drill the 3/8" through hole first and then turn them. The problem I'm having is with the thicker ones.
I've tried any number of ways to hold these. I've tried glueing them to the dowel first and clamping that in a chuck. I've tried turning a wooden faceplate with a dowel epoxied into it to register the dowel hole on the piece I'm turning and using double sided tape to hold it to the faceplate.
But these are small, and I'm hollowing pretty deeply without a lot of room and catches happen. When they do, the piece usually is knocked off-center and I have to sort of start over with it. Not to mention the damage done to the dowel if I've glued the whorl on already and am holding that dowel to turn.
I've thought about this a lot, and I don't recall seeing any other way to turn these whorls except for making a little tapered wood button pin and hammering that into the dowel hole and clamping the other side in a chuck. My worry is that doing so will wallow out the dowel hole a bit, and I'd rather use 3/8" birch dowels that I taper for these rather than turning a shaft from scratch. So, the dowels are just under 3/8" already. I don't have any more room for slop. And the button would get in the way of hollowing, making it hard to turn the center post cleanly.
I don't know if a 3/8" collet chuck might do a better job of holding it securely while I turn if I glue the whorl on the dowel first. But I don't have a collet chuck anyway!

Here's my current idea, and I thought I'd run it by y'all and see if you have any critiques or other suggestions. I suspect y'all will know of ways I just haven't come across yet.
I'm thinking of expoxying a length of 3/8" threaded rod into a 1" dowel I turn so that I can clamp it in a chuck, say one with 70mm jaws so there's a nice register for the face of the piece I'm turning. Then, I could drill a hole through a short length of 1/2" or 3/4" dowel as a bushing and put a washer and nut on the other side, so that when I tighten the nut, I clamp the piece I'm turning between the jaws of the chuck and the wood bushing in the center in front. Would this work?
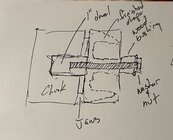
Is there a better way to do this, short of learning how to use my bowl gouge better so I don't have catches?
