I applied a few coats of Watco's Danish Oil to a bowl made of Western Alder, which is not quite a hardwood. This was a twice turned bowl which I had slowly drying for a year. Sanded to 600 grit and applied the oil and wiped. Now after a couple of days I notice some areas have this surface fuzziness about them which, if you wipe your hand across the surface in one direction disappears (see lower photo where I've wiped a finger on one section).
How do I eliminate what are obviously tiny fibers? 000 steel wool? a polishing compound like ultra-shine? I intend to apply a final finish of bees wax.
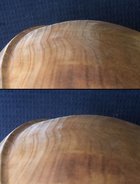
How do I eliminate what are obviously tiny fibers? 000 steel wool? a polishing compound like ultra-shine? I intend to apply a final finish of bees wax.
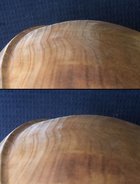