Just a quick introduction. I am a collector of sorts, lately a number of Classical Indian instruments have made it into the old cabinet of curiosities.
I am working on a restoration of an instrument called a Sarangi, and it requires tuning pegs. LOTS of tuning pegs (literally 41).
I thought I would share my first forays into this woodturning craft.
The market price for a set of replacement pegs seems pretty steep all in one chunk, so I took another route that would allow me to make my own.
In the beginning I showed a finished peg to a mentor, who commented "what a waste of wood".
His idea being that it was a shame to take a nice piece of Mahogany and whittle away 75% of it leaving basically the knob and a small shaft.
His take was to turn the knobs and shafts separately, to save wood. I also realized this brought the potential to make knobs from a variety of exotic woods.
So, here's my take on his take.
Start with some small Mahogany Stock, in this case 3/4" x 3/4" x 6" pieces to use for the shafts.
Find some exotic hardwood to use for knobs. For this first group I chose African Blackwood, similar to Ebony. 2" x 2" x 12"
I hope not to offend those of expertise and knowledge, I am admittedly a rank beginner. At least these instrument pegs are pretty simple as you can see.
Cheers and thanks in advance for all of the knowledge I hope to glean from this Forum.
Patrick

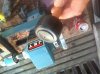
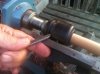
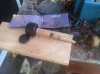
I am working on a restoration of an instrument called a Sarangi, and it requires tuning pegs. LOTS of tuning pegs (literally 41).
I thought I would share my first forays into this woodturning craft.
The market price for a set of replacement pegs seems pretty steep all in one chunk, so I took another route that would allow me to make my own.
In the beginning I showed a finished peg to a mentor, who commented "what a waste of wood".
His idea being that it was a shame to take a nice piece of Mahogany and whittle away 75% of it leaving basically the knob and a small shaft.
His take was to turn the knobs and shafts separately, to save wood. I also realized this brought the potential to make knobs from a variety of exotic woods.
So, here's my take on his take.
Start with some small Mahogany Stock, in this case 3/4" x 3/4" x 6" pieces to use for the shafts.
Find some exotic hardwood to use for knobs. For this first group I chose African Blackwood, similar to Ebony. 2" x 2" x 12"
I hope not to offend those of expertise and knowledge, I am admittedly a rank beginner. At least these instrument pegs are pretty simple as you can see.
Cheers and thanks in advance for all of the knowledge I hope to glean from this Forum.
Patrick

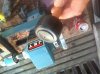
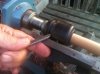
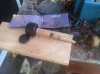