Actually two questions.
As a new turner, I've turned a number of bowls from cherry, ash and elm. Thus far my finishing process has been using walnut oil, then Yorkshire Grit, then two coats of Tried and True Danish oil then two coats of T&T Original. Seems very nice (cherry live edge and darker elm in photo), but very flat, even a bit "furry" feeling....though that is exaggerating. Maybe its dust, as those have been sitting a while now!
For the latest bowl (lower right - elm I think, from a downed tree on my property), I tried Mylands Cellulose Sanding Sealer. Sanded to 400, used the sealer, burnished with steel wool, then did the Yorkshire Grit process, which adds some oil and wax to the piece and then gets buffed out. The piece looks really nice right now (light elm in photo), and it much smoother than a similar piece of elm using the previous process (the darker elm in picture).
My main question is, what to do now with the latest bowl? Am considering trying T&T Varnish. Or maybe just buff with the usual three compounds, adding more wax?
Second question would be, any suggestions for improvement to that first process? maybe using the sealer in there as well?
As a newbie, the zillion finishing options are pretty confusing! And so many opinions out there.
Thanks for any advice.
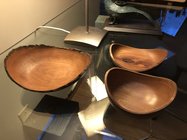
As a new turner, I've turned a number of bowls from cherry, ash and elm. Thus far my finishing process has been using walnut oil, then Yorkshire Grit, then two coats of Tried and True Danish oil then two coats of T&T Original. Seems very nice (cherry live edge and darker elm in photo), but very flat, even a bit "furry" feeling....though that is exaggerating. Maybe its dust, as those have been sitting a while now!
For the latest bowl (lower right - elm I think, from a downed tree on my property), I tried Mylands Cellulose Sanding Sealer. Sanded to 400, used the sealer, burnished with steel wool, then did the Yorkshire Grit process, which adds some oil and wax to the piece and then gets buffed out. The piece looks really nice right now (light elm in photo), and it much smoother than a similar piece of elm using the previous process (the darker elm in picture).
My main question is, what to do now with the latest bowl? Am considering trying T&T Varnish. Or maybe just buff with the usual three compounds, adding more wax?
Second question would be, any suggestions for improvement to that first process? maybe using the sealer in there as well?
As a newbie, the zillion finishing options are pretty confusing! And so many opinions out there.

Thanks for any advice.
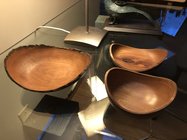