I am experimenting with a big scrap of wood I had in the shop. I have it attached with a woodworm screw in my Nova chuck. I am trying to approximate a wing bowl, and so far I think I'm having some success. As I have progressed in turning, I have found a bark inclusion(?) that is a pretty deep hole:
My question is: should I fill it, or try and keep turning to up with a hole in the finished piece? I guess I would just have to keep my tools super sharp to do the latter. If I try and fill it, what should I use? I've never attempted anything like this before.
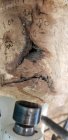
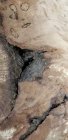