john lucas
AAW Forum Expert
What I call my fan mirrors have always been an incredibly difficult thing to glue up. What you basically have is a whole bunch of wedge shaped pieces. So when you put glue on and make it slippery all the pieces want to go every which way.
The veneer also acts like a spring which compounds the problem. What I did today was to prebend the veneer to match the shape of each section. I did this using curling iron and heat bent it. This made the whole thing fit together without the spring action pushing it apart.
Then I built this jig to push on each section. it's just angle iron welded together and tapped for the socket head screws. It worked even better than I hoped. Before snugging it up very far I was able to push the veneer down towards the bottom. Then when I cranked each screw it pushed the wedges down toward the bottom It was very easy and quite satisfying. Now all I have to do is turn the mirror.
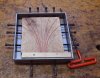
The veneer also acts like a spring which compounds the problem. What I did today was to prebend the veneer to match the shape of each section. I did this using curling iron and heat bent it. This made the whole thing fit together without the spring action pushing it apart.
Then I built this jig to push on each section. it's just angle iron welded together and tapped for the socket head screws. It worked even better than I hoped. Before snugging it up very far I was able to push the veneer down towards the bottom. Then when I cranked each screw it pushed the wedges down toward the bottom It was very easy and quite satisfying. Now all I have to do is turn the mirror.
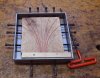
Attachments
Last edited: