Haven't posted in a while. Lots of things have been happening to keep me out of the wood shop and off the lathes.
But You may ( or not ) recall my exploration of a shop built version of the Munro hollower. Well I just had my preconceptions handed to me.
Take a look at this image from the MWCTA site under "What's it"
http://www.mwtca.org/images/stories/whats_it_column/160-5.jpg
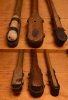
I rather suspect that this is a shielded cutter. They say they are lathe tools.
I guess everything old is new again.
But You may ( or not ) recall my exploration of a shop built version of the Munro hollower. Well I just had my preconceptions handed to me.
Take a look at this image from the MWCTA site under "What's it"
http://www.mwtca.org/images/stories/whats_it_column/160-5.jpg
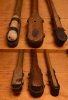
I rather suspect that this is a shielded cutter. They say they are lathe tools.
I guess everything old is new again.