I've got a couple of taller hollow forms (12 to 14 inches) that both have a nub at the bottom. It's about 1/2 inch long, maybe a 1/4 inch wide, a bit fuzzy looking, and dead center in the bottom of my forms. If it matters, they're both maple. I'm using Trent Bosch's stabilizer and 3/4 inch tools for the hollowing. All that happens when I get my tool down on the nub is it bounces around, never seeming to cut any of it.
Is there a secret tool I don't know about that can reach 12 to 14 inches down a narrow opening and snip it off?
I'm not sure how visible it will be, but I attached an image of the nub, looking straight down into the vessel.
All suggestions are welcome and appreciated.
Grey
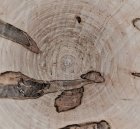
Is there a secret tool I don't know about that can reach 12 to 14 inches down a narrow opening and snip it off?
I'm not sure how visible it will be, but I attached an image of the nub, looking straight down into the vessel.
All suggestions are welcome and appreciated.
Grey
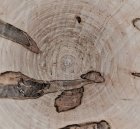