Hi folks,
I know there are coring systems for bowl blanks.
However I have a kind of odd need. I’m making a cylinder for a kitchen utensil canister. I’m gluing several square blocks of cherry together and turning it round on the lathe to about 6 1/2 inches.
I don’t want to waste the cherry wood on the inside of the canister by hollowing it out in the normal fashion.
Is there a way to core a cylinder from the inside of this block to use for other projects?
I’m thinking of pushing a sharp diamond shaped carbide tool straight into the block at 3” from the center line to core out the center cylinder. Then I’ll glue a base on the utensil canister.
Would this work? Is there a better tool available for this, or can I make one from an HSS shaft?
The images below are of the first utensil canister I made by laminating multiple oak boards then hollowing the block out in the usual fashion, but it wasted a tremendous amount of good wood.
(I’m developing a way to use parallel staves to make the cylinder with canoe joints made on my router to join them but I haven’t gotten that completely figured out yet. See last photo. But I need to complete a utensil canister soon for a friend.)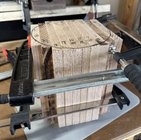
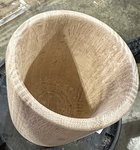
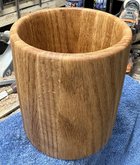
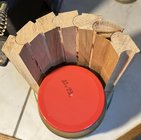
I know there are coring systems for bowl blanks.
However I have a kind of odd need. I’m making a cylinder for a kitchen utensil canister. I’m gluing several square blocks of cherry together and turning it round on the lathe to about 6 1/2 inches.
I don’t want to waste the cherry wood on the inside of the canister by hollowing it out in the normal fashion.
Is there a way to core a cylinder from the inside of this block to use for other projects?
I’m thinking of pushing a sharp diamond shaped carbide tool straight into the block at 3” from the center line to core out the center cylinder. Then I’ll glue a base on the utensil canister.
Would this work? Is there a better tool available for this, or can I make one from an HSS shaft?
The images below are of the first utensil canister I made by laminating multiple oak boards then hollowing the block out in the usual fashion, but it wasted a tremendous amount of good wood.
(I’m developing a way to use parallel staves to make the cylinder with canoe joints made on my router to join them but I haven’t gotten that completely figured out yet. See last photo. But I need to complete a utensil canister soon for a friend.)
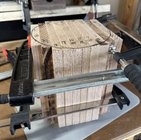
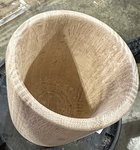
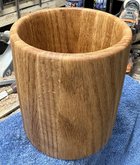
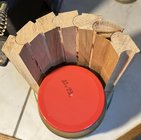