I've been able to successfully combine my CNC with my turnings for embellishment. I still have to work on my creativity like many. The usual problem with applying a CNC to woodturnings are the curves in 2 or more directions. I have used some expensive programs which 'sort of' do this by wrapping a design around the Y axis while using a 4th (or A) axis. This technique works fine for cylinders but comes up very short for a real turned object decoration. With a bowl for example, a laser will lose focus and a router bit will not carve as you want it too if you stray very far from a flat-ish area or rim.
I was inspired by the work of John Lucas with his router platform (recently featured in the AAW magazine), and Jeff Salter with his jig more than a year ago. However I was not happy with either of these approaches for a variety of reasons. I also looked at the very fine work of Bill Ooms and his ornamental lathe approach but I don't have that setup.
There are a variety of Open Software offerings that do similar Y axis image wrapping but once again I was not happy with the limitations of that approach.
Last summer I started more fully exploring a program called Grblgru to use with my CNC. Working with the author, some refinements were made and I am happy to say that I can do pretty much whatever I want to do with any of my turnings now. Best of all this software is Free. In fact you don't even need a CNC to experiment with it, just a Windows computer. The Gcode can be saved easily.
The author originally designed this program to be an educational simulation and added a GCode sender to it as time went on. This can directly operate machines that run on GRBL 1.1 (Arduino Uno) or Grbl-Mega-5X (Arduino Mega 2560) for example. This doesn't work with dedicated Laser burners because they don't work like a regular CNC with a 4th axis. It doesn't work with a Mach 3/4 machine but these could run the generated GCode.
These are two small test forms I made to test Grblgru's ability to follow the curves. As you can see the curves were very well followed. The carving on the left took about 5 minutes, on the right about 10 minutes. Total time to scan a form like this is about 1 to 2 minutes. Since I am an impatient turner this suits me just fine. If I chose to use a laser to burn an image the results are the same. I use a simple 6 watt diode laser which does a more than adequate job of burning into the wood even at half power.
The process is simple: scan the form shape, create a virtual model of it, apply a design and embellish in about 15 min total with practice.
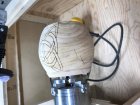
This image I stretched to cover the test curve and left the laser line thick to illustrate how both curves are followed. My 4th axis is a simple one I made using a Nema24 stepper motor, bearings, 8mm shaft and a 1" bolt. My Z axis probe cost me all of a dollar. I take my scroll chuck off the lathe and spin it on to the 4th axis. These things don't have to be expensive and most CNC machines can be used but the owner has to climb a learning curve like anything else. Although ultimately straightforward, this is a method that is best with some understanding of how your CNC really works. This solution is inexpensive and effective in my experience.
I was inspired by the work of John Lucas with his router platform (recently featured in the AAW magazine), and Jeff Salter with his jig more than a year ago. However I was not happy with either of these approaches for a variety of reasons. I also looked at the very fine work of Bill Ooms and his ornamental lathe approach but I don't have that setup.
There are a variety of Open Software offerings that do similar Y axis image wrapping but once again I was not happy with the limitations of that approach.
Last summer I started more fully exploring a program called Grblgru to use with my CNC. Working with the author, some refinements were made and I am happy to say that I can do pretty much whatever I want to do with any of my turnings now. Best of all this software is Free. In fact you don't even need a CNC to experiment with it, just a Windows computer. The Gcode can be saved easily.
The author originally designed this program to be an educational simulation and added a GCode sender to it as time went on. This can directly operate machines that run on GRBL 1.1 (Arduino Uno) or Grbl-Mega-5X (Arduino Mega 2560) for example. This doesn't work with dedicated Laser burners because they don't work like a regular CNC with a 4th axis. It doesn't work with a Mach 3/4 machine but these could run the generated GCode.
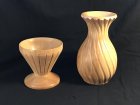
These are two small test forms I made to test Grblgru's ability to follow the curves. As you can see the curves were very well followed. The carving on the left took about 5 minutes, on the right about 10 minutes. Total time to scan a form like this is about 1 to 2 minutes. Since I am an impatient turner this suits me just fine. If I chose to use a laser to burn an image the results are the same. I use a simple 6 watt diode laser which does a more than adequate job of burning into the wood even at half power.
The process is simple: scan the form shape, create a virtual model of it, apply a design and embellish in about 15 min total with practice.
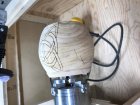
This image I stretched to cover the test curve and left the laser line thick to illustrate how both curves are followed. My 4th axis is a simple one I made using a Nema24 stepper motor, bearings, 8mm shaft and a 1" bolt. My Z axis probe cost me all of a dollar. I take my scroll chuck off the lathe and spin it on to the 4th axis. These things don't have to be expensive and most CNC machines can be used but the owner has to climb a learning curve like anything else. Although ultimately straightforward, this is a method that is best with some understanding of how your CNC really works. This solution is inexpensive and effective in my experience.