I know that woodturning and the term "precision" really don't go well together due to the nature of wood movement. I don't sell my boxes, nor do I ever intend to do so. I don't want a loose fitting lid. I like a good suction or snap fit lid.
Currently, box making is my go to activity on the lathe. I enjoy the opportunity to make the lid fit as precise as possible. However, I realize that the precision of fit probably won't matter because the wood will move, some types more than others. Nevertheless, it gives me satisfaction to make an as "perfectly" round as possible lid to base fit (at least while on the lathe or for a few minutes after I take it off the lathe), I judge this by being able to twist the lid 360 degrees around on the base and the friction is the same all the way around.
I have attached photos of a single piece of maple that is approx. 1.5" x 1.5" (kiln dried). One photo shows tight grain while the other shows wider grain. When the box is rounded, of course, the tight grain and the wide grain alternate.
I have found, in my quest for "perfection" that the tighter grain is slightly deeper than the wider grain portions of the cylinder. In other words, if I lightly touch my tool rest against the wide grain and slowly rotate the spindle by hand the slight sound of the rubbing between the tool rest and the cylinder at the wide grain almost disappears when I get to the tight grain. What causes this variance?
We all try to line up the lid grain to the box grain. Usually, the fit is perfect when the lid and the box grain is lined up. I have noticed, especially when boxes have sat for a little time (some woods longer than others), if I try to turn the lid on the box, the fit will tighten and then loosen up as it rotates. In other words, when the lid tight grain matches up with the box wide grain, the fit is tighter than when all the grain lines up. What causes this variance?
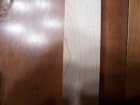
Currently, box making is my go to activity on the lathe. I enjoy the opportunity to make the lid fit as precise as possible. However, I realize that the precision of fit probably won't matter because the wood will move, some types more than others. Nevertheless, it gives me satisfaction to make an as "perfectly" round as possible lid to base fit (at least while on the lathe or for a few minutes after I take it off the lathe), I judge this by being able to twist the lid 360 degrees around on the base and the friction is the same all the way around.
I have attached photos of a single piece of maple that is approx. 1.5" x 1.5" (kiln dried). One photo shows tight grain while the other shows wider grain. When the box is rounded, of course, the tight grain and the wide grain alternate.
I have found, in my quest for "perfection" that the tighter grain is slightly deeper than the wider grain portions of the cylinder. In other words, if I lightly touch my tool rest against the wide grain and slowly rotate the spindle by hand the slight sound of the rubbing between the tool rest and the cylinder at the wide grain almost disappears when I get to the tight grain. What causes this variance?
We all try to line up the lid grain to the box grain. Usually, the fit is perfect when the lid and the box grain is lined up. I have noticed, especially when boxes have sat for a little time (some woods longer than others), if I try to turn the lid on the box, the fit will tighten and then loosen up as it rotates. In other words, when the lid tight grain matches up with the box wide grain, the fit is tighter than when all the grain lines up. What causes this variance?
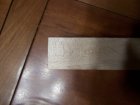
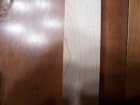