There is the vibration your lathe will produce at any given rpm and combine that with the vibration a chunk of wood spinning will produce at any given rpm......along with the effect a sharp tool has on the vibration at that rpm. If you can control all those things, it's possible to get a perfectly clean tearout free cut......provided the tool is sharp and the presentation of that tool is correct.
It cannot be stressed how much rpm effects the cleanest of cuts, and rpm must be adjusted precisely.
It also cannot be stressed enough just how much sharpness contributes to the "perfect cut".
One very good method of infinitely adjusting the rpm beyond what us mere mortals can is with a vibrometer.
You can't buy one of these, but you can easily make one, and here is a thread that will tell you how:
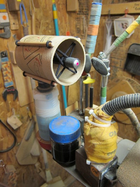
=o=
It cannot be stressed how much rpm effects the cleanest of cuts, and rpm must be adjusted precisely.
It also cannot be stressed enough just how much sharpness contributes to the "perfect cut".
One very good method of infinitely adjusting the rpm beyond what us mere mortals can is with a vibrometer.
You can't buy one of these, but you can easily make one, and here is a thread that will tell you how:
I am looking for ideas for devices, or inventions for detecting minor vibrations on the lathe.
The purpose is to adjust the rpm to where the least possible vibrations are present.
Right now, I use my fingertips on the lathe bed, plus there is one long neck spot lamp that consistently gives me some good indications. Other lamps and fixtures on the headstock also help.
Assuming the best location would be connected to the headstock, but entertaining input, if any.
I have tried an antennae like affair that was not very successful.
I also have experimented with a jar of water, that was...
The purpose is to adjust the rpm to where the least possible vibrations are present.
Right now, I use my fingertips on the lathe bed, plus there is one long neck spot lamp that consistently gives me some good indications. Other lamps and fixtures on the headstock also help.
Assuming the best location would be connected to the headstock, but entertaining input, if any.
I have tried an antennae like affair that was not very successful.
I also have experimented with a jar of water, that was...
- Odie
- Replies: 103
- Forum: Woodturning Discussion Forum
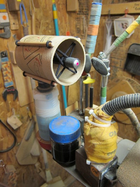
=o=