Bitten by the basket illusion bug, I have been thinking for some time about trying to turn a Yokut Indian rattlesnake basket as a not too distant future project. These were used in ceremonies where the snake was introduced via a cylindrical opening. The problem is how can I bead the interior of the wide mouth cylinder, since it's visible? I’m using a midi-lathe so the diameter of the basket must not exceed 10” to 11”; that makes the snake entry about 5 1/2 “ wide at most and 2” deep. It’s obvious to me that one can cheat (improvise
) a bit by making the top of the basket as a lid, but that still leaves the visible part of the cylinder to bead. I would guess that I need to make a bent tool. Any ideas from the experienced basket illusion makers? I believe Jim Adkins made one (or more ?) of these. As a help I’ve made a rough sketch of such a design below.
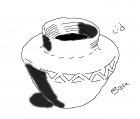

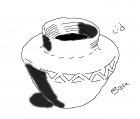