Yes I have a lot to learn still and once a our new house and I get my new shop up and running I'll give this greenwood turning a better go of it.
It seems to cut very easy / smooth when green and from what I gather you need to submerge the piece in DNA to drive out the moisture and then dry slowly in bags etc?
Bruce, it is true, turning green wood is addictive ... especially if you cut some green wood in early spring. It will sling water all over you and your shop and it turns like butter.
Personally, I would forget about using alcohol. It is very expensive and unnecessary. On the other hand, there are some turners who swear by it. I see it as one of those topics like politics and religion that are sure to arouse a spirited debate. I did some searching a few years ago and found some technical papers from the early twentieth century on using ethyl alcohol to help stabilize lumber. The gist of what I found wasn't about speeding up drying, but rather improving yield by increasing the plasticity of the lignin in the cell walls in order to reduce internal stresses that cause of warping, bowing, end checking, and other drying defects. It appears that the idea never got traction in the lumber industry probably because it wasn't cost effective. From what I remember, it was necessary to use extremely high pressure to get the alcohol to penetrate to a sufficient depth.
The main requirement for air drying wood is that it needs to be dried slowly to minimize warping and splitting -- the slower, the better. That is why woodturners use Anchorseal, melted wax, and bagging among other things to slow down the drying rate of rough turned pieces. On wood that is prone to moving and cracking, I use Anchorseal. I turn a lot of mesquite which doesn't need any kind of special treatment. It is is very stable and a wet piece can be turned to completion in one session without the need for rough turning followed by air drying that most other species of wood require.
I have also turned some white oak which is plentiful around here and love the character that it has, but it also just loves to split wide open at the slightest provocation. My solution to that problem is to find old dead trees that have some great figure and accept the existing cracks as a part of the character of the wood.
Here is a hollowform that is an example of FOG (found on ground) post oak. It was about as hard as a rock to turn, but I love the figure in the wood. All of the cracking had taken place years before I turned it so I didn't have to worry about what was going to happen after it was turned.
BTW, the oak in your layered vessel does have spectacular figure and I can see why you chose to make a turning out of it. I can envision it as a beautiful centerpiece on a coffee table holding a flower arrangement. On one hand, Richard made a valid a point about the discontinuities caused by layering pieces tend to pull the viewer's focus away from the overall piece, but depending on the intended use of the piece, the layers can also work in favor the piece. I'm in favor of encouraging new turners doing their own exploration of various ideas while also engaging in mutual sharing of ideas enabling us to gain even greater opportunities to think outside the box. Something that I have been wanting to try for a long time and that I think you would be interested in as a way to feature the highly figured white oak in a layer bowl is covered in an article titled, "Layered Bowls" by Jim McPhail in Volume 20, Issue 4 of of American Woodturner. If you are an AAW member, you can download any back issue of the journal as one of the member benefits. In essence, the article presents some design ideas using contrasting thin accent layers that help feature the character of figured wood. Here is a screen shot of one of the layered bowls in the article.
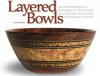