Hello again,
Now I must apologize for this post because I know there is so many variables involved but I'm having a very hard time and could use some help.
I am cutting some Staghorn Sumac with a natural edge, it's a fairly small blank, maybe 6-1/2"x4-1/2" deep. It's green wood and very wet, I have never heard of sumac growing this big but it looked interesting to me so I bought a couple blanks from eBay. I have an 8" diameter piece of this as well, but I wanted to practice on the small one. I will attach some pictures to show the torn grain, I just can't seem to get rid of it no matter what tool I try? I tried taking a nice slow finish pass with my 1/4" bowl gouge. freshly sharpened at 45° degrees. I tried all my bowl gouges ranging from 45° to 60° degrees. The smallest gouge worked the best for finish but the grain is really torn. I have tried my negative rake scrapers, regular scrapers, spindle gouges, nothing works?
I hate sanding more than torn grain so I would like to try and figure this out if possible. I was running the lathe speed at 800 and tried all the way to about 2200 RPM, all pretty much had the same results. If anyone has ever cut this stuff or if anyone has any tips I would be forever grateful!
Thank you, I hope everyone is having a great Saturday! It's cold and rainy so a perfect day to stay in the shop and turn all day!
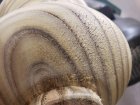
Now I must apologize for this post because I know there is so many variables involved but I'm having a very hard time and could use some help.
I am cutting some Staghorn Sumac with a natural edge, it's a fairly small blank, maybe 6-1/2"x4-1/2" deep. It's green wood and very wet, I have never heard of sumac growing this big but it looked interesting to me so I bought a couple blanks from eBay. I have an 8" diameter piece of this as well, but I wanted to practice on the small one. I will attach some pictures to show the torn grain, I just can't seem to get rid of it no matter what tool I try? I tried taking a nice slow finish pass with my 1/4" bowl gouge. freshly sharpened at 45° degrees. I tried all my bowl gouges ranging from 45° to 60° degrees. The smallest gouge worked the best for finish but the grain is really torn. I have tried my negative rake scrapers, regular scrapers, spindle gouges, nothing works?
I hate sanding more than torn grain so I would like to try and figure this out if possible. I was running the lathe speed at 800 and tried all the way to about 2200 RPM, all pretty much had the same results. If anyone has ever cut this stuff or if anyone has any tips I would be forever grateful!
Thank you, I hope everyone is having a great Saturday! It's cold and rainy so a perfect day to stay in the shop and turn all day!
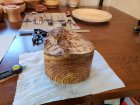
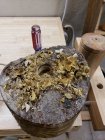
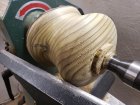
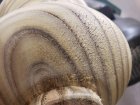