I am completely new to woodturning. I got a old 12 inch craftsman lathe and got it set up and one of the first things I noticed is the tool rest was at an angle. I moved the foodstock up and it lines up perfectly with the headstock. The foot end of the toolrest is probably an inch lower. I rotated the tool rest 180 degrees and the foot end is still lower. I removed the tool rest and banjo and it seems the main part on the beam is unlevel. There is no slop to it. I measured foot side compared to the head and there is probably an 1/8 inch difference in height. The only thing I can think of is it was a bad casting from the factory or craftsman put this angle on it for some reason. My best solution is to grind it down and file it flat. Am I missing something here?
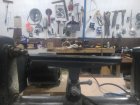
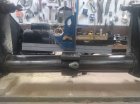
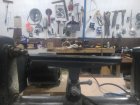