I was at a meeting of the Etowah River Woodturners and was admiring the finish on another members project. On asking about it I got an invite to come see the process. Turns out Ron Comtois had added a small dc motor to an old Delta lathe so he could mount a piece on it and leave it rotating at 16 rpm while applying and drying the poly finish resulting in a dead smooth surface.
I figured I could cobble something together for myself and only having the one lathe I would build an accessory drive that can be mounted and dismounted easily.
I got a used reduction motor off ebay for a few bucks that had a speed control board with it. Only big hurdle was how to transfer the power to my chuck. Fortunately I was looking online at Northern tool at their reasonably priced pulleys and belt and found what I needed. First was a two inch pulley with a half inch hole to fit the gearmotor, then there was a six inch pulley I planned to cut the hub out of and machine the hole to fit the lathe and a 37” v belt to hook it up.
After I got it home I had the extreme good fortune to find the big pulley had a core welded into a 1 1/4” hole, exactly the size needed so all it took was cutting the weld off and tapping the piece out.
So far I dont have a permanent mount yet. I took a board and clamped it to the bed and clamped the motor to it. The pulley went on the head behind the chuck and tightened up a bit. Slipped the belt on, snugged it and applied power. I was able to set the speed right on the money.
All I need now it to build the mounting of the platform for the motor and put the control board into a box with the control knob mounted on it.
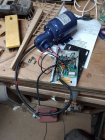
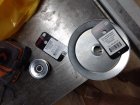
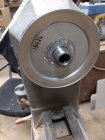
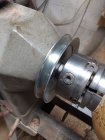
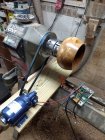
I figured I could cobble something together for myself and only having the one lathe I would build an accessory drive that can be mounted and dismounted easily.
I got a used reduction motor off ebay for a few bucks that had a speed control board with it. Only big hurdle was how to transfer the power to my chuck. Fortunately I was looking online at Northern tool at their reasonably priced pulleys and belt and found what I needed. First was a two inch pulley with a half inch hole to fit the gearmotor, then there was a six inch pulley I planned to cut the hub out of and machine the hole to fit the lathe and a 37” v belt to hook it up.
After I got it home I had the extreme good fortune to find the big pulley had a core welded into a 1 1/4” hole, exactly the size needed so all it took was cutting the weld off and tapping the piece out.
So far I dont have a permanent mount yet. I took a board and clamped it to the bed and clamped the motor to it. The pulley went on the head behind the chuck and tightened up a bit. Slipped the belt on, snugged it and applied power. I was able to set the speed right on the money.
All I need now it to build the mounting of the platform for the motor and put the control board into a box with the control knob mounted on it.
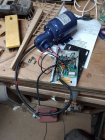
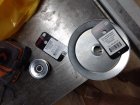
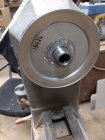
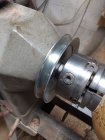
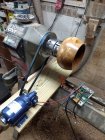