I recently came across these "unique" salt & pepper mills at a dinner party. As I have been spending some time studying Barbara Dill's articles and videos in my endeavor to learn the techniques of multi axis spindle turning, I was wondering if @barbara dill or, any forum members could give me any guidance on how to turn similar shapes to use for salt & pepper mills.
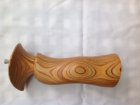
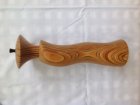

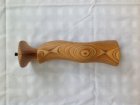
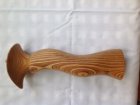
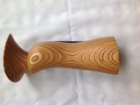
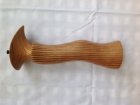
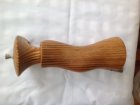
The big challenge for me is how to achieve the core hole through the centre of the spindle whilst turning the perimeter shapes. I haven't been able to work out yet the positioning, and number of axes to be used to end up with a turning that will accommodate the conventional Danish grind mechanisms.
I have uploaded 4 photos each of the shorter salt mill (205 mm) and the taller pepper mill (255 mm) which show 4 aspects of each mill's turning.
Any tips or suggestions will be highly appreciated.
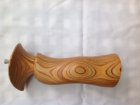
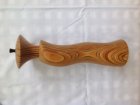

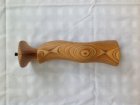
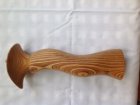
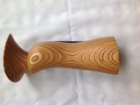
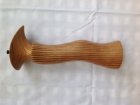
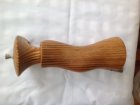
The big challenge for me is how to achieve the core hole through the centre of the spindle whilst turning the perimeter shapes. I haven't been able to work out yet the positioning, and number of axes to be used to end up with a turning that will accommodate the conventional Danish grind mechanisms.
I have uploaded 4 photos each of the shorter salt mill (205 mm) and the taller pepper mill (255 mm) which show 4 aspects of each mill's turning.
Any tips or suggestions will be highly appreciated.
Last edited by a moderator: