- Joined
- Jul 18, 2018
- Messages
- 1,272
- Likes
- 2,667
- Location
- Baltimore, MD
- Website
- loujacobswoodturning.com
I’m making some large buttons for my daughter who is knitting a sweater. I wonder if anyone has experience or thoughts about a good finish that may stand up to periodic cleaning, or is that simply impossible? Also, grain orientation. While I like this look, I wonder if making them parallel to the grain (flat-grained) might offer less opportunity for water being absorbed. This one is ash, but I imagine an oilier wood like teak, rosewood, etc., might be a better choice.
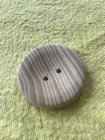
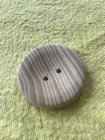