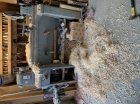
There are two main questions I have, and they may be related to one another so I'll put them both here.
One involves the set up of my lathe, and stalling, the other is a bouncing tool.
Bear with me through some background.
My lathe is a Rockwell Delta 12" gap bed lathe, circa 1972, Power is a 3ph .75 hp motor with a Teco 510 VFD. The lathe has a reeves drive - the cable version. Speeds go from about 350 to 3000 or so through the Reeves, and with the VFD, can go down to nothing. Upon receiving the lathe, I dismantled it, replaced bearing in head stock, tail stock, and I think the reeves drive as well.
I'm finding that I can stall the lathe pretty easily when first roughing a bowl blank. Mounting the wood so that the ends at the tailstock and headstock are side grain. As I make my first cuts across the blank, from tailstock to headstock, it seems to stall occasionally. FWIW, much more frequently on the headstock end. When this happens, I can see the wheel on the left side of the headstock is stopped, telling me the slippage is underneath, with the belts. Might this be caused by insufficient belt tension? When I got the machine, I don't know the belts were correct for it.
Second related question, when roughing across the blank, as well as when evening out the face grain on the tailstock end, I'm constantly fighting the bounce/chatter. Just can't seem to get a smooth flow. It feels like I'm fighting the cut, and I'm definitely using more pressure than is described in the various videos, where they are able to easily and smoothly make this cut. I've tried a number of ways of rotating the tool, as well as the angle of the handle, trying to follow the bevel. This bouncing occurs with both push cuts and scraping cuts. At this point, I've got past it my using the tip more and taking much smaller bites. The only obvious difference is that I'm using a 3/8" bowl gouge, while most seem to want a half inch - measured across the flutes, not the shaft diameter. I'm not adverse to buying more tools, but at same time, figure that if I can't make the cut with the gouge I have, just getting a bigger chisel means I can't make the cut with it either.
Obviously seeing something in person would be ideal, but given circumstances, that will have to wait.
Thanks
Last edited: