I've finally achieved 1" thickness in the northern hemisphere (the hole end) - the southern hemisphere (faceplate end) is a bit over 2" as you get near the bottom.
I must confess, I find it mesmerizing to stare into the cavernous interior of this log. The inside diameter is about 30", larger than any outside diameter piece I've turned by 8".
The pic was taken with a 180-degree Nikon fisheye - the distortion is an unavoidable by-product. The camera-man is Randy Smith, without whom the lathe modifications would have failed a long time ago and the whole project would have cratered - turning a grossly out-of-balance 1000-lb log is precarious and dangerous. Thanks to Randy this project still may succeed.
Hopefully I'll get it into the drying room in a week or so, after which I'm planning on turning a few weed-pots.
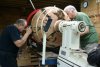
I must confess, I find it mesmerizing to stare into the cavernous interior of this log. The inside diameter is about 30", larger than any outside diameter piece I've turned by 8".
The pic was taken with a 180-degree Nikon fisheye - the distortion is an unavoidable by-product. The camera-man is Randy Smith, without whom the lathe modifications would have failed a long time ago and the whole project would have cratered - turning a grossly out-of-balance 1000-lb log is precarious and dangerous. Thanks to Randy this project still may succeed.
Hopefully I'll get it into the drying room in a week or so, after which I'm planning on turning a few weed-pots.
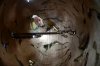
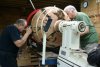