I am new to this forum and thought I would introduce myself. I am retired and located in Haubstadt Indiana ( just north of Evansville Indiana ). I have been turning for about 6 years, ther first 4 years making pens, pepper mills, bottle stoppers, etc. I then had a 3 year break retiring and building a new house and shop in Haubstadt. I have three lathes, a Delta LA 200, Jet 1014VS, and a Powermatic 90 that I bought at a school auction before moving. I raised the PM 90 so I have a 18" swing, that is ideal for me. The last two years I am expanding to do bowls and larger items, however I enjoy all turning and want to do minatures someday. I am a member of a turning club and recently joined the AAW and this forum. I have also signed up to attend the AAW Symposium in Kanas City. My goal here is to gain insight from more experienced turners and new ideas. I think the gallery and tips section are great.
Advice to new turner; join a woodturning club if possible, watch videos from multiple turners on the same subject/technique. One may click and another won't.
My PM 90
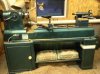
Some of my turnings
The first two are a small lidded box made from Blackwood and Pink Ivory, the second two are a combination of Blackwood and resin with pearlex and filled with brass shavings
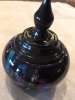
This bowl is hickory and the band is amber transtint
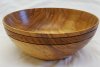
This is the crematory where some of my turnings end up. This is why I want to get better.
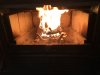
Edit: I sold my PM 90 June 2017. The PM 90 is a great lathe, however even after my many updates there were still features I did not have. Many choices, but I settled on the Laguna Revo 18-36 and have been very happy with the performance of this lathe. I added 280 lbs. sand ballast and a place for my frequent used lathe accessories. I also have a place to lay my tools instead of on the lathe ways.
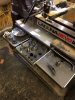
Advice to new turner; join a woodturning club if possible, watch videos from multiple turners on the same subject/technique. One may click and another won't.
My PM 90
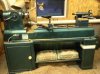
Some of my turnings
The first two are a small lidded box made from Blackwood and Pink Ivory, the second two are a combination of Blackwood and resin with pearlex and filled with brass shavings
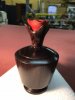
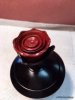
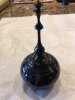
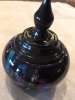
This bowl is hickory and the band is amber transtint
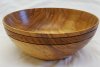
This is the crematory where some of my turnings end up. This is why I want to get better.
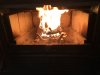
Edit: I sold my PM 90 June 2017. The PM 90 is a great lathe, however even after my many updates there were still features I did not have. Many choices, but I settled on the Laguna Revo 18-36 and have been very happy with the performance of this lathe. I added 280 lbs. sand ballast and a place for my frequent used lathe accessories. I also have a place to lay my tools instead of on the lathe ways.
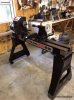
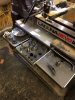
Last edited: